MATERIALS & PROCESSES
At the start of each project I work out a colour palette and use stains and oxides to colour the porcelain for inlaying. I then form slabs with white or black porcelain and inlay the coloured images or patterns. Shapes are cut from these slabs and vessels are hand formed while the porcelain is still soft. Offcuts are used to reform slabs creating new patterns and in this way I ensure I do not waste any materials as even the smallest pieces are reused.
ENVIRONMENTAL MEASURES
Environmental awareness and sustainable production are very important to me, so I have adopted a ‘closed loop’ approach to my practice, recycling and reusing as much material from my ceramic production as possible. Firing porcelain in my kiln uses a lot of energy, so I’m always trying new ways to create vibrant colours at lower temperatures.
My ceramics are always carefully considered, one-off pieces, to add value and meaning to my practice. My Beloved Cherry Tree is a body of work that commemorates the beautiful old cherry tree that stood in my garden until the wild storms of 2019 took it down. A stark reminder that the climate crisis is affecting us all. This work celebrates the beauty of nature while also reminding us of the urgent need to take better care of the world we inhabit.
JEWELLERY
I created a collection of jewellery to make the best use of every last little piece of my hand made inlaid porcelain, to be as sustainable and resource efficient as possible in my practice. Every piece is a one off, each individual bead is unique and earrings have creatively considered mismatched pairings. All packaging is hand made using recycled card.




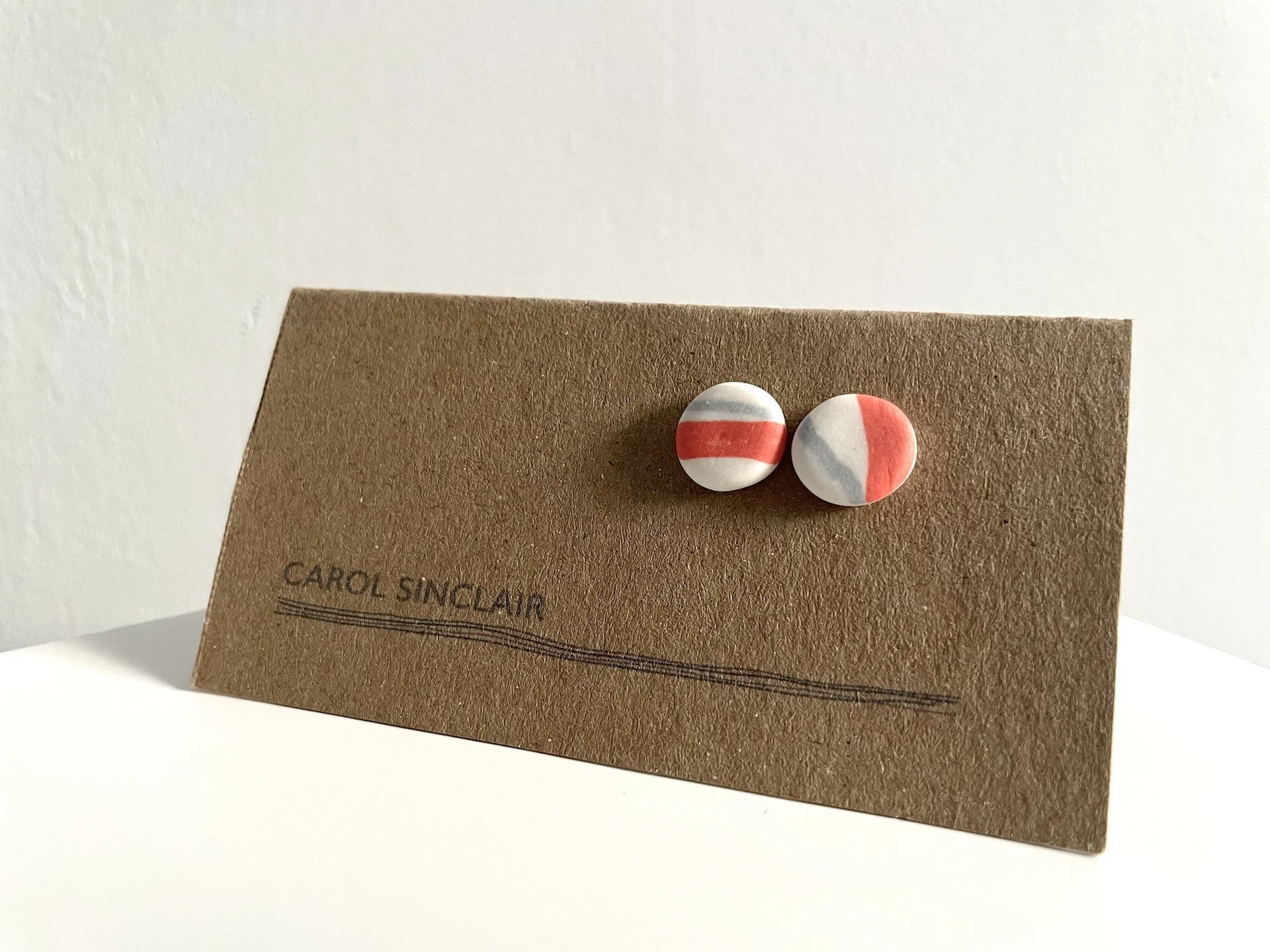
